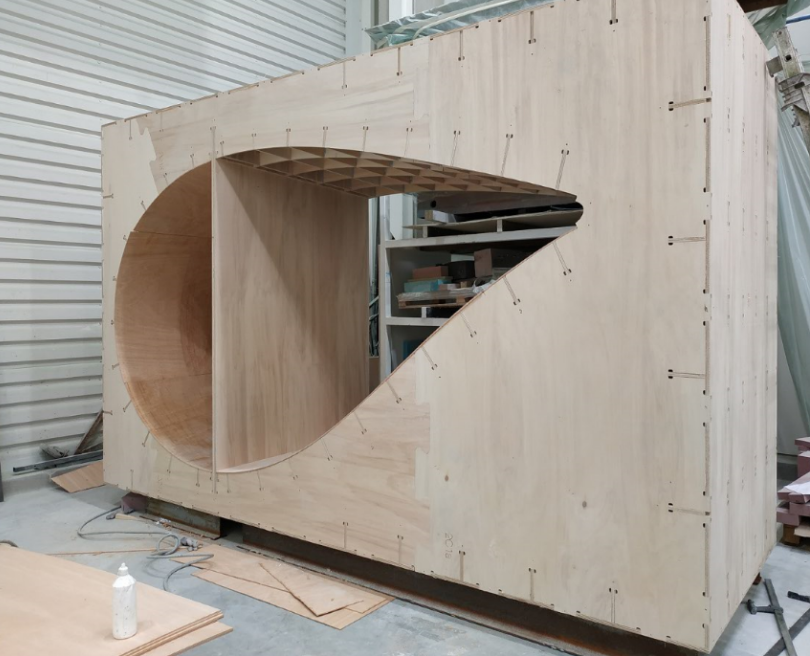
Background
The last few decades have been marked by a decline of the Levelized Cost of Energy (LCOE) produced from wind turbines. This decrease is mainly due to the reduction cost of manufacturing wind turbines. To further continue this downward trend in LCOE, the maintenance has to be performed at the right time in order to maximize power production time on the whole life of the power generation system. This is particularly true for offshore wind turbines where maintenance costs are significantly higher than those incurred in operations on the Onshore turbines.
To maximize the production leverage, Structure Health Monitoring (SHM) has been proved one of the routes to explore. Indeed, its aim is to replace common preventive maintenance, with a more efficient and cost-effective “condition based” or “predictive” maintenance. This approach demands a proper instrumentation of the structure to monitor, which allows its health status during operation and can detect the occurrence and/or evolution of a defect in time.
The goal of RIVERS project is to assess the relevance of a solution for the structure health monitoring of large offshore wind turbine composite blade, based on Digital Image Correlation (DIC) technique. More specifically, RIVERS will work on i) design and build an optical measurement system meant to be permanently installed within wind turbine blade and ii) develop an image processing algorithm to able spotting delamination and/or local cracks when they occur. This approach has to be reasonably affordable to be employed in any blade.
Figure below shows the measurement area on a wind turbine blade and the experimental test bench as well as the imaging equipment. The industrial-sized composite blade was mounted on a large concrete base to support it in a cantilevered position for static and fatigue loading.
The RIVERS project is financed by Nantes Métropole within the framework of the WEAMEC Call for Projects “Petits Matériels”.
Scientific advances and innovation
- Development of monitoring solution based on DIC method
- Development of a robotic camera positioning structure to scan the inner surface of the blade
- Automatic generation of alert messages
Expected technical and economic impact
The project results should enable the industrial to optimize and thus reduce the costs of its maintenance operations based on the health status monitoring and also on eventual alerts received, rather than periodic preventive maintenance. The technology developed can also be employed in other industrial sectors for large structures monitoring.
Key project milestones
- June 2019 - Launch of the project
- September 2019 - Definition of the defects to be monitored
- January 2020 - Development of the detection system on a mock-up
- September 2020 - Test results at a representative scale
- September 2021 - Optimization of data processing
- October 2021 - End of the project
Demonstrator
Monitoring solution developed in project will be evaluated during test scheduled in a real blade.
Prospects
The skills acquired during this project will enable the IRT Jules Verne to offer another option of SHM solutions to other industrial sectors by adapting this solution to other specific contexts and needs.